Demand for recycled polyethylene terephthalate (PET), or recycled polyester, has increased significantly in recent years. There are many advantages to recycled polyester, including reduced energy consumption in the manufacturing process as compared to producing virgin polyester; reduced CO2 emissions, and reduced extraction of crude oil and natural gas to make virgin plastic. There are two techniques for producing recycled polyester: mechanical recycling and chemical recycling also known as advanced recycling.
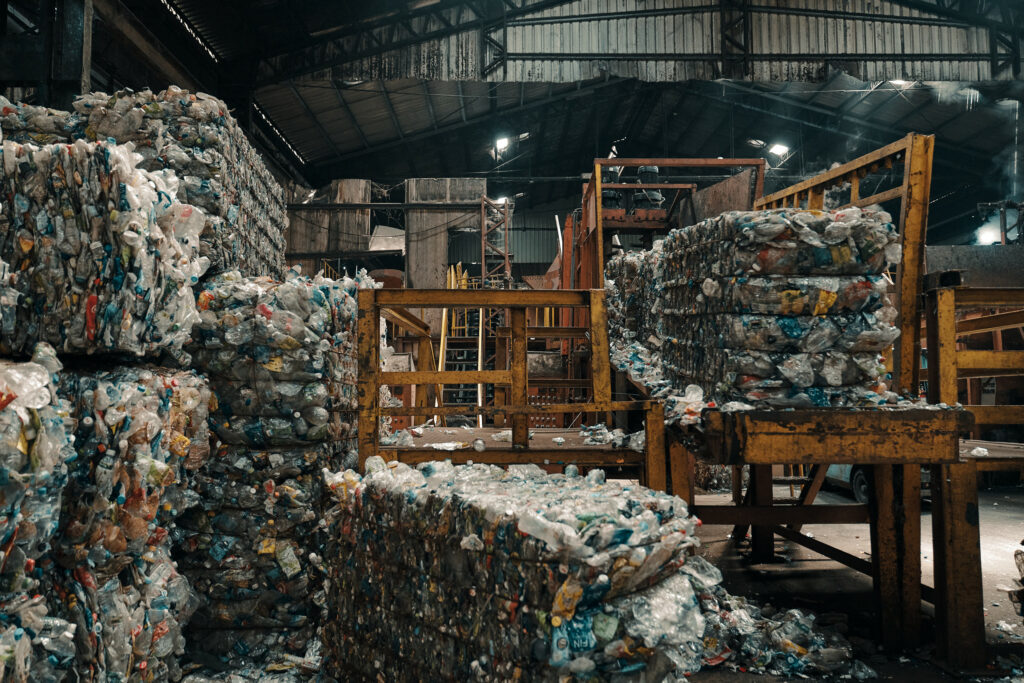
Mechanical versus Chemical Recycling
Mechanical recycling involves shredding recycled PET bottles and pressing the flakes into consistently shaped pellets that are melted and extruded into recycled polyester fiber. Mechanical recycling requires no chemicals, save for detergents to clean the original recycled material, but the process can weaken the fiber which then must be mixed with virgin fiber to result in acceptable strength. To date, mechanical recycling is the most affordable and widely used process to produce recycled polyester.
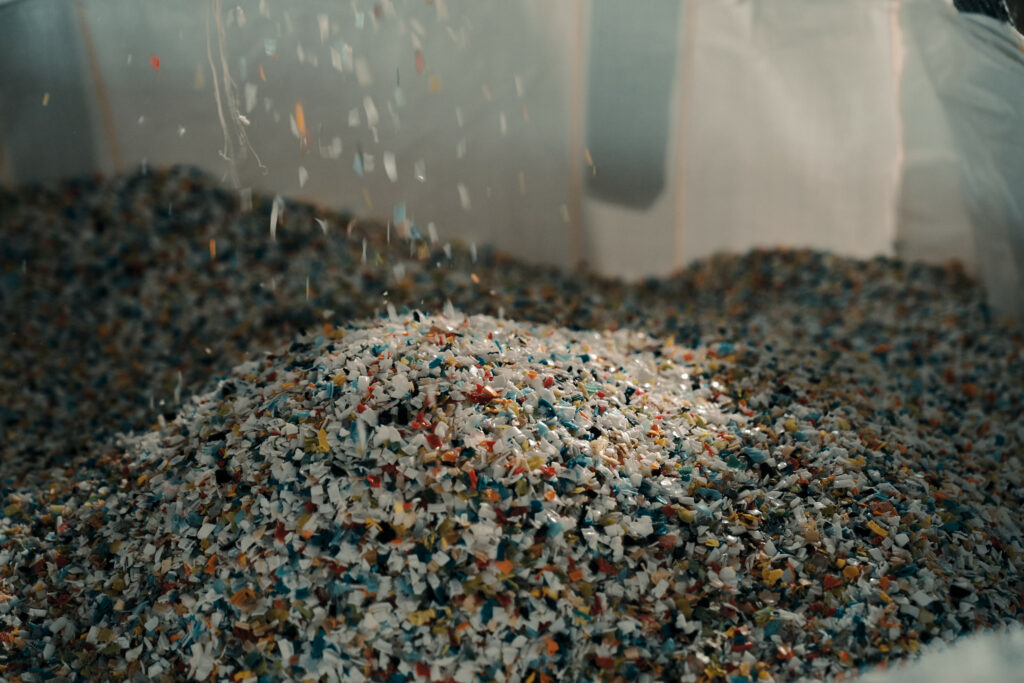
Chemical recycling uses a chemical process to break down PET products into their molecular parts so that they can be reformed into a yarn of equal strength. Unlike mechanical recycling, the quality of the chemically recycled polyester remains consistent and does not degrade its performance. However, chemical recycling is currently more expensive than the alternative and must be scaled up to achieve more widespread adoption.
Advanced Recycling Technologies
In addition to chemical recycling, or depolymerization, industry experts are constantly investigating new and innovative methods for recycling plastics. The industry refers to these technologies as “Advanced Recycling Technologies,” a term established by the American Chemistry Council (ACC). According to the ACC, the term advanced recycling accomplishes two things: it identifies technologies that go deeper into the polymer than the mechanical recycling process and it also confirms that these processes are, indeed, a form of recycling, even though they differ from traditional recycling. There are three main methods of advanced recycling:
Purification, which use a solvent or chemical to precipitate the polymer out of a solution, leaving behind colorants, additives, and other contaminants. Some of the most common types of purification include solvent extraction and chromatography. Pros: Purification results in a clean and clear polymer and removes contaminants, colorants, and additives. This results in a recycled product that has many of the characteristics of virgin polymers. Cons: Purification does not restore the polymer to its virgin molecular level, which means that it retains the heat history of melting and remelting and can alter the molecular weight and viscosity of the plastic. Purification is also more energy intensive than mechanical recycling, but less than chemical recycling.
Depolymerization, which breaks the chemical bonds in the complex chains that make up polymers. In this process, additives and colorants are separated from chemicals and monomers, the latter of which can be put back into reactors to make a recycled polymer identical to its virgin counterpart. Pros: The recycled polymer is identical to its virgin counterpart. Cons: The technology is not currently operating at scale, and when it does, there will be a need for massive quantities of materials to be recycled than are currently available. Also, the technology currently has a higher environmental footprint than mechanical recycling.
Conversion reprocesses plastic products into other sellable, tradable commodities. Pros: Once proven and scaled, conversion technology could prevent massive amounts of plastics from ending up in landfills or the world’s oceans. Cons: Not every repurposed product can be considered recycled. To meet the standard of being recycled, the new product must be reprocessed into materials instead of fuels or energy.
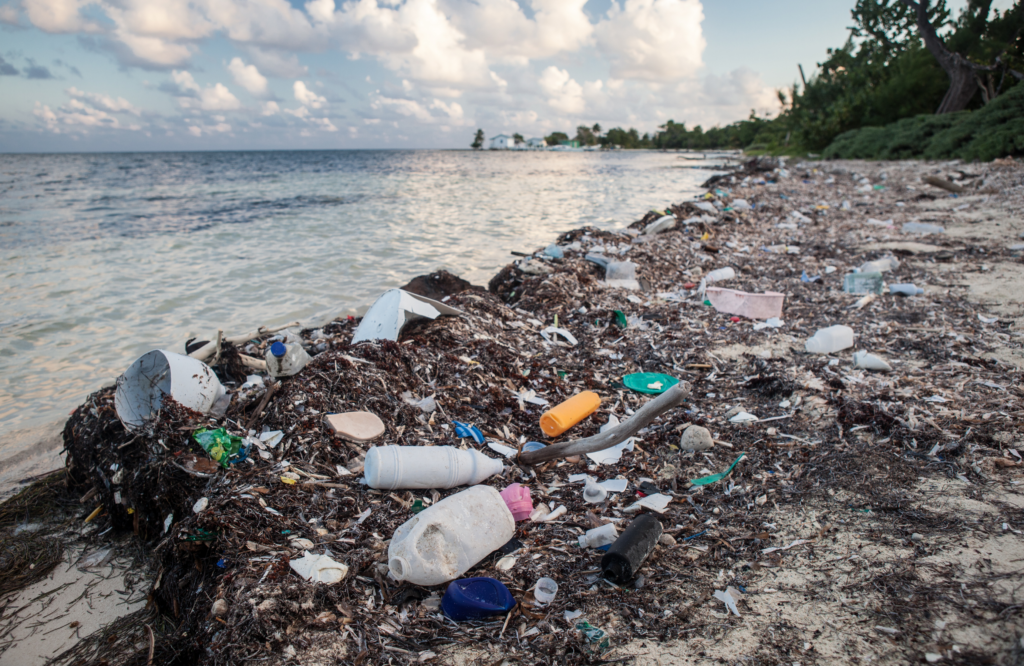
Even though these technologies are still emerging and innovating, recycling plastic is preferable to using virgin components. The most common way to recycle plastic is through mechanical recycling, but that process degrades the product’s quality over time. Chemical recycling preserves the quality of the original material but is expensive and has a larger environmental footprint. Nevertheless, manufacturers are demanding more recycled materials, which is driving innovation and allowing producers to scale up current technologies. Eventually, recycling plastics will allow us to keep polymers out of trash streams and will allow us to continue to produce necessary and valuable products without using virgin materials.
To share your thoughts on recycled polyester or to learn more about SAYA fiber, please contact us at change@sayarenew.com